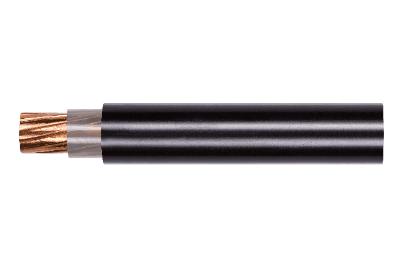
Polyethylen (PE) wird häufig verwendet in derIsolierung und Ummantelung von Stromkabeln und TelekommunikationskabelnAufgrund seiner hervorragenden mechanischen Festigkeit, Zähigkeit, Hitzebeständigkeit, Isolierung und chemischen Stabilität ist PE ein sehr gutes Material. Aufgrund seiner strukturellen Eigenschaften ist seine Beständigkeit gegen Spannungsrisse jedoch relativ gering. Dies ist besonders dann problematisch, wenn PE als Außenmantel von großflächigen Panzerkabeln verwendet wird.
1. Mechanismus der Rissbildung in der PE-Hülle
Risse in der PE-Ummantelung treten hauptsächlich in zwei Situationen auf:
a. Umweltbedingte Spannungsrissbildung: Hierbei handelt es sich um das Phänomen, dass der Mantel aufgrund kombinierter Spannungen oder der Einwirkung von Umweltmedien nach der Installation und dem Betrieb des Kabels spröde Risse an der Oberfläche erleidet. Die Ursache hierfür sind hauptsächlich innere Spannungen im Mantel und längerer Kontakt mit polaren Flüssigkeiten. Umfangreiche Forschungen zur Materialmodifizierung haben diese Art von Rissbildung weitgehend behoben.
b. Mechanische Spannungsrisse: Diese entstehen durch strukturelle Mängel im Kabel oder ungeeignete Mantelextrusionsverfahren und führen zu erheblichen Spannungskonzentrationen und verformungsbedingten Rissen während der Kabelinstallation. Diese Art der Rissbildung ist in den Außenmänteln von großflächigen, mit Stahlband gepanzerten Kabeln stärker ausgeprägt.
2. Ursachen für Risse im PE-Mantel und Verbesserungsmaßnahmen
2.1 Einfluss des KabelsStahlbandStruktur
Bei Kabeln mit größerem Außendurchmesser besteht die Panzerung typischerweise aus doppellagigen Stahlbandumwicklungen. Je nach Kabelaußendurchmesser variiert die Stahlbanddicke (0,2 mm, 0,5 mm und 0,8 mm). Dickere Panzerstahlbänder weisen eine höhere Steifigkeit und eine geringere Plastizität auf, was zu größeren Abständen zwischen den oberen und unteren Schichten führt. Beim Extrudieren führt dies zu deutlichen Unterschieden in der Manteldicke zwischen den oberen und unteren Schichten der Panzerungsoberfläche. Dünnere Mantelbereiche an den Rändern des äußeren Stahlbandes erfahren die größte Spannungskonzentration und sind die Hauptbereiche, in denen später Risse entstehen.
Um den Einfluss des gepanzerten Stahlbandes auf den Außenmantel zu mildern, wird eine Pufferschicht bestimmter Dicke zwischen das Stahlband und den PE-Mantel gewickelt oder extrudiert. Diese Pufferschicht sollte gleichmäßig dicht und ohne Falten oder Vorsprünge sein. Das Hinzufügen einer Pufferschicht verbessert die Glätte zwischen den beiden Stahlbandlagen, gewährleistet eine gleichmäßige PE-Manteldicke und reduziert in Kombination mit der Kontraktion des PE-Mantels die innere Spannung.
ONEWORLD bietet Benutzern verschiedene Dicken vonverzinktes Stahlband, gepanzerte Materialienum den unterschiedlichsten Bedürfnissen gerecht zu werden.
2.2 Einfluss des Kabelproduktionsprozesses
Die Hauptprobleme beim Extrusionsprozess von gepanzerten Kabelummantelungen mit großem Außendurchmesser sind unzureichende Kühlung, unsachgemäße Formvorbereitung und ein zu hohes Streckverhältnis, wodurch zu hohe innere Spannungen in der Ummantelung entstehen. Aufgrund ihrer dicken und breiten Ummantelungen sind große Kabel in Extrusionsproduktionslinien häufig hinsichtlich Länge und Volumen der Wasserrinnen begrenzt. Das Abkühlen von über 200 Grad Celsius während der Extrusion auf Raumtemperatur ist eine Herausforderung. Unzureichende Kühlung führt zu einer weicheren Ummantelung in der Nähe der Panzerungsschicht, was beim Aufwickeln des Kabels zu Kratzern auf der Manteloberfläche und schließlich durch äußere Kräfte zu potenziellen Rissen und Brüchen beim Verlegen des Kabels führt. Zudem trägt unzureichende Kühlung nach dem Aufwickeln zu erhöhten inneren Schrumpfkräften bei, wodurch das Risiko von Mantelrissen unter erheblichen äußeren Kräften steigt. Um eine ausreichende Kühlung sicherzustellen, wird empfohlen, Länge oder Volumen der Wasserrinnen zu vergrößern. Es ist wichtig, die Extrusionsgeschwindigkeit zu senken, gleichzeitig die richtige Plastifizierung des Mantels aufrechtzuerhalten und während des Aufwickelns ausreichend Zeit zum Abkühlen zu lassen. Da Polyethylen ein kristallines Polymer ist, trägt eine segmentierte Abkühlungsmethode mit Temperaturreduzierung von 70–75 °C auf 50–55 °C und schließlich auf Raumtemperatur dazu bei, innere Spannungen während des Abkühlungsprozesses abzubauen.
2.3 Einfluss des Wickelradius auf die Kabelwicklung
Beim Aufwickeln von Kabeln halten sich Hersteller an Industriestandards zur Auswahl geeigneter Lieferrollen. Die Anpassung an lange Lieferlängen bei Kabeln mit großem Außendurchmesser stellt jedoch eine Herausforderung bei der Auswahl geeigneter Rollen dar. Um die angegebenen Lieferlängen einzuhalten, reduzieren manche Hersteller die Trommeldurchmesser, wodurch die Biegeradien für das Kabel unzureichend werden. Übermäßiges Biegen führt zu Verschiebungen in den Panzerungsschichten und damit zu erheblichen Scherkräften auf den Mantel. In schweren Fällen können die Grate des gepanzerten Stahlbandes die Polsterschicht durchdringen, sich direkt in den Mantel einbetten und Risse oder Spalten entlang der Kante des Stahlbandes verursachen. Beim Verlegen des Kabels führen die seitlichen Biege- und Zugkräfte dazu, dass der Mantel entlang dieser Spalten reißt, insbesondere bei Kabeln, die näher an den inneren Schichten der Rolle liegen, wodurch sie bruchanfälliger werden.
2.4 Einfluss der Bau- und Installationsumgebung vor Ort
Um den Kabelbau zu standardisieren, wird empfohlen, die Verlegegeschwindigkeit zu minimieren und übermäßigen Seitendruck, Biegungen, Zugkräfte und Oberflächenkollisionen zu vermeiden, um eine zivilisierte Bauumgebung zu gewährleisten. Lassen Sie das Kabel vor der Installation vorzugsweise bei 50–60 °C ruhen, um innere Spannungen im Mantel abzubauen. Vermeiden Sie längere direkte Sonneneinstrahlung auf Kabel, da Temperaturunterschiede auf verschiedenen Seiten des Kabels zu Spannungskonzentrationen führen und das Risiko von Mantelrissen während der Kabelverlegung erhöhen können.
Veröffentlichungszeit: 18. Dezember 2023